What are progressive cavity pumps?
Progressive cavity pumps, also known as PC pumps, progressing cavity pumps, eccentric screw pump and mono pumps are a type of rotary positive displacement pump designed for the conveying of liquids and sludges from 1cst to 1Million. They handle not only viscous fluids and solids but also gassing or multiphase liquids containing gas slugs typical during crude oil extraction.
The volume of liquid pumped is proportional to speed providing a linear predictable pumping rate across a range of pressures. This technology delivers one of the highest flow and pressures available from a positive displacement pump being up to 600M³H and 48bar, with efficiency ranging from 55% to 75%. This technology is most suited for fluids more viscous than 5cst.
What is the design of a progressing cavity pump and working principle?
The design consists of a motor at the drive end which is connected to a gearbox as pc pumps operate at low rpm compared to centrifugal pumps. The output shaft from the gearbox connects to a rotor via a universal pin joint which rotates a metallic rotor within a rubber stator. Stators contain cavities, and the rotor pushes fluids through the cavities in a slow rotating fashion.
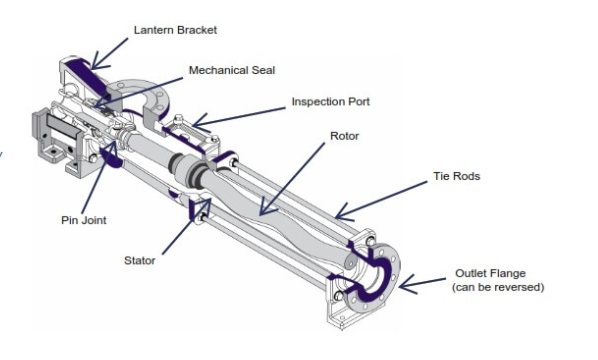
A pumps pressure generating ability will depend on the number of cavities within the pump, with high pressure designs often consisting of more than one stator and rotor. Each rotor will typically produce 6 bar enabling pressures up to 48 bar to be achieved through its modular design.
The clearances between the rotor and stator are very small thus meaning any fluids which are transferred must be lubricating, within a consistent temperature band as the stator can expand at certain temperature bands leading to stator scoring or damage if the two contact.
This design of pump is better suited for viscous lubricating fluids, which can contain solids. Short stator life can be experienced with abrasive slurries at which point a peristaltic pump can be a preferred option. Eccentric Screw Pumps viscosity handing is unrivalled, and they are usually specified when there are no other suitable options.
Rotors are usually a range of metals from cast iron, and tool steel, to stainless steels and duplex’s which at times are hardened to cater for aggressive and/or high-pressure applications. Hollow rotors allow for higher operating speeds, long life spans, produce low vibration and near silent running.
Stator designs consist of two types – equal and non-equal walled. Equal walled stators ensure a lower starting and running torque, lower pulsations and reduced power consumption, high volumetric pumping efficiency, and lower replacement costs. Materials are usually types of rubber being NBR, FKM but not PTFE meaning solvents cannot be handled.
Applications for units can be found across a range of industries and include:
- Wastewater – Thickened & Treated Sludge Transfer & Polymer dosing.
- Oil & Gas – Cutting Transfer, Drilling Mud transfer and recovery, Separator Feed, Crude Oil Transfer, MOL (Main Oil line Pump), Multiphase transfer and injection in remote areas.
- Biogas – Digestate feed & Biomass transfer.
- Paper and Pulp – Pulp Transfer, recycled paper transfer, Filler transfer, fixative & dye metering.
- Edible Oil – Crusher feed, Oil Malaxing (mixing), oil extraction, oil separator feed, filter press feed.
- Wine – Wine filtering, grape pressing, must & pomace transfer.
Pump curve
PC Pump curves are different to a centrifugal curve as it is linear demonstrating the units ability to handle liquids of varying viscosities with little impact on pump performance, with the bottom axis being speed rather than flow as flow is proportional to speed. Unit speed is much lower than centrifugal, operating from as little as 50rpm
progressive cavity pump curve sludge/progressive cavity pump performance curves
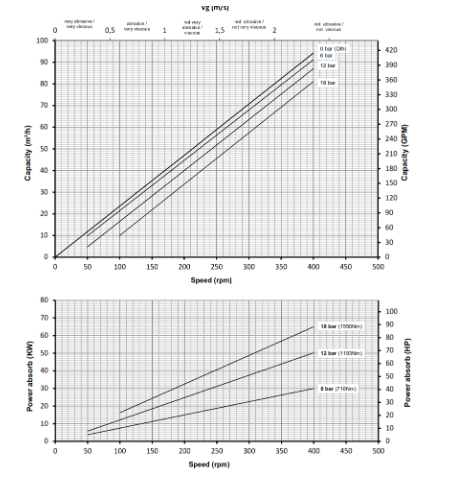
Progressing Cavity Pump Efficiency
Progressing Cavity Pump Efficiency refers to the ability of a progressing cavity pump to effectively convert input power into fluid flow. Factors such as pump design, operating conditions, and fluid properties influence the efficiency of the pump. High-efficiency progressing cavity pumps can deliver greater flow rates with lower energy consumption, resulting in cost savings and reduced environmental impact.
People Also Ask